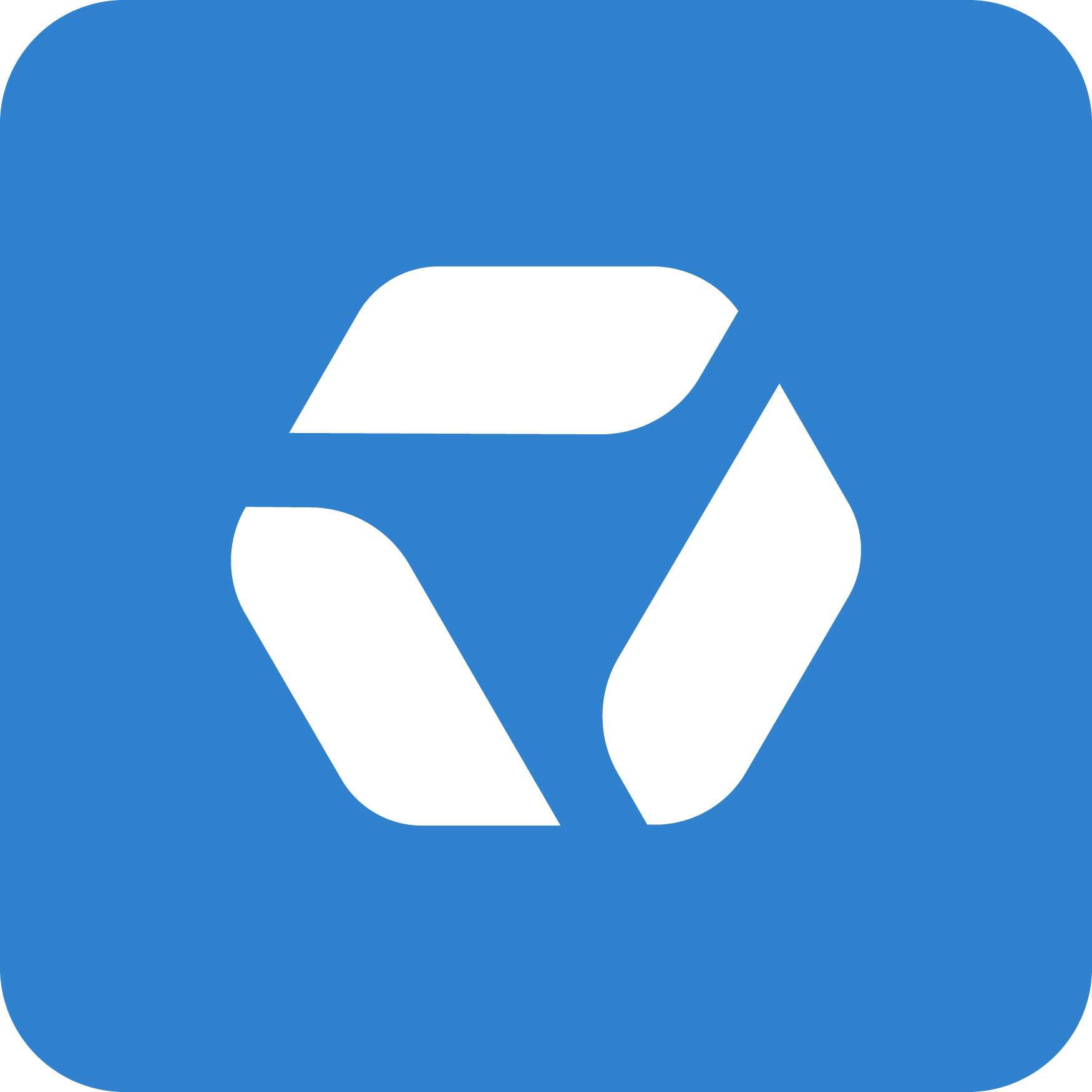
Elena Ravencourt
Aug 27, 2023
•
9
min read
•
48
votes
•
Articles
Inventory refers to the things you own and desire to sell through your business. Inventory management is the process of monitoring and storing items to efficiently and quickly meet customer demand. It pertains to the methods you use to get, store, and prepare goods for sale.
Investments include inventory. The implications of poor inventory control may not become apparent for weeks or months. Once they do, it won't be a pretty sight: moldy goods, dead stock, expensive preservation, or more seriously, low supply and unmet client orders. Additionally, holding expenses and storage fees can reduce your profitability.
Unsold products and materials kept for resale to both internal customers (such as other university units) and external customers (i.e., customers outside the University of Illinois System) are recorded as inventory for resale, a general ledger asset, at the lowest of cost or market value. Merchandise held for resale, publications held for resale (such as books, journals, pamphlets, etc.), raw materials used to make a product for resale, finished/unfinished items stored for resale, etc. are a few examples of inventory for resale.
You must have a thorough understanding of each step in the inventory management process before creating an inventory management plan. This is essential for minimizing error and selecting the best inventory management program for your company.
Economic order quantity (EOQ) is a formula that determines how much inventory a business should buy based on a number of parameters, including total production costs, demand growth, and more. In order to reduce purchasing, holding, and other expenditures, the formula determines the most units.
The least amount of inventory that a retail company will buy in order to keep costs down is known as the minimum order quantity (MOQ). The MOQ for inventory products with higher production costs is frequently lower than for simpler, less expensive, and more accessible things, so bear that in mind.
Using the ABC analysis approach, you can arrange your inventory starting with the most crucial products and working your way down to the least crucial ones. The B products are valuable but are ordered just once a month whereas the A items are the highest priority stock and need to be replenished frequently. The C products are low-stock priority items that are frequently carried in large quantities and don't require frequent reordering. Using ABC analysis to arrange your stock will help you make the most of your available storage space and speed up fulfillment.
In actuality, providers make errors. You'll encounter problems like unrecorded stock, unexpected stock outages, and payments for items you never purchased if you don't have a tried-and-true process for inspecting and recording incoming products to detect faults and damage. Count products against purchase orders, follow up with suppliers regarding any errors, shortages, or damages, completely unpack whole shipments, and update stock counts in your inventory management system to verify the correctness of your stock receipts.
Although it is possible, manually managing your inventory is tiresome, time-consuming, and dangerous. You can quickly automate many of your procedures, track the movement of your inventory, and expand to more physical locations via the Internet if you utilize a single, top-notch inventory management software or point-of-sale (POS) system. This may result in fewer mistakes, more effectiveness, and higher productivity.
One of your most valuable resources is your supplier base. After all, you wouldn't be able to produce or sell goods and make money without them. To keep children informed of what happens to their possessions once they leave their hands is a smart idea. You might be able to lock in discounts, lower the possibility of delays and quality problems, and streamline your inventory management by developing strong connections with them. Don't be scared to replace problematic or underperforming suppliers with new ones.
The bare minimum of inventory you must have in your warehouse at all times is referred to as the minimum stock threshold. You'll be prepared to handle an unanticipated increase in sales if you can figure out what this amount is and keep enough stock on hand. By meeting demand, you'll lower the chance of lengthy fulfillment waits, which could harm your reputation.
By using the just-in-time (JIT) inventory management strategy, businesses can avoid dead stock items that were placed on sale but were never purchased or used by customers by only ordering what they actually need.
LIFO and FIFO are the two methods used to determine the cost of products. First-in, first-out, sometimes known as FIFO, is the theory that older stock is sold first to maintain it’s current. In order to stop the stock from spoiling, LIFO, or last-in, first-out, assumes that the more recent inventory is usually sold first.
The reorder point formula determines the bare minimum of stock that a company should hold before placing another order. To account for lead time, a reorder point is typically higher than a safety stock number.
In order to track inventory expiration or track down defective items, users can group and monitor similar commodities using the batch tracking quality control technique.
You're absolutely correct if you're picturing your neighborhood consignment shop at this point. Consignment inventory is when a vendor or wholesaler agrees to deliver their goods to a consignee without the consignee making an upfront payment for the inventory. The products are still owned by the consignor who is supplying the inventory, and the consignee only pays for them when they are sold.
Dropshipping is a type of order fulfillment where the provider sends the customer's order directly from the supplier. Instead of selecting the item from their own stock when a store makes a sale, they buy it from a third party and have it shipped to the customer.
Any business practice can benefit from implementing the comprehensive set of management techniques known as lean manufacturing. By removing waste and any other non-value-adding activities from daily operations, it seeks to increase efficiency.
The Six Sigma methodology equips businesses with the tools they need to raise performance (earnings) and reduce excess inventory.
Lean Six Sigma improves Six Sigma's tools but places a greater emphasis on improving word standardization and business flow.
In order to predict client demand, demand forecasting is based on historical sales data. In essence, it's a projection of the products and services a business anticipates its clients will buy in the future.
In order to achieve a JIT shipping process, cross-docking is a procedure where products are directly unloaded onto outbound vehicles from a supplier truck. Because of this, there is basically no need for storage in between deliveries.
Internally, streamlining procedures should lead to increased effectiveness and facilitate a smoother and simpler deployment of any newly introduced systems or procedures. Teams can always stand to gain from assessing and enhancing current working methods, whether it be for task allocation, quality control, or project monitoring. Streamlining is the process of making something simpler or more effective. This occurs when a process or approach used to complete a task is reformed in order to increase its general effectiveness and/or efficiency in producing outcomes. For instance, by ensuring that the process steps are consistently and frequently followed by any one person in charge of creating and dispersing the bills, the work of billing clients can be expedited.
Any sequence of repetitive tasks carried out by an individual or group, in a particular order, to achieve a goal is referred to as a business process. Each of these actions is a task, which may be an independent occurrence or a step in a process. Different organizations will have different levels of formal business processes, with the formal procedures being documented. Regardless of formality, a simplified business process produces faster results and, ideally, causes fewer problems or inefficiencies along the way.
Not many organizations are fully aware of the scope of their current processes, whether they are formal or informal. Therefore, the first step in streamlining processes is to always make a list of all procedures and then analyze each one in depth. You must be familiar with how each procedure in every department or unit of your business works. During this phase, it will be determined how the business has been performing thus far and where prospects for improvement exist. Interview staff members and get their opinions on each procedure your company does.
After analyzing your current work procedures, you must then decide which areas want improvement. Search for procedures and workflows that have dwindling employee motivation, fuzzy instructions, or deteriorating communication. Identify the elements that may or may already be affecting the efficiency of the current processes and set improvement goals.
Breaking the work process down into smaller, more manageable parts is the next step once a process has been identified as needing improvement. Due to their overly convoluted work processes, too many firms get bogged down in the dependencies and decision-making processes of all of their projects. Keep the process straightforward by dividing it into distinct parts that only seek to get the intended result.
After identifying and deconstructing the processes that require change, you must prioritize them. On a scale of 1 to 10, with 1 being the most significant procedure and 10 being the least important process, evaluate the processes on your list. This makes it clear when resources are needed and keep priorities in focus.
It comes as no surprise that current work management software solutions are one of the most widely used tools businesses employ today to manage their workflow in a world of rapid technological innovation. Data errors and misunderstanding might happen during the process of completing a task or project. But there are a tonne of effective software tools available that are made to support teams and organisations in streamlining their operations. These contemporary management software options include straightforward tools and apps with cutting-edge capabilities, simplifying the challenging task of controlling corporate processes more than ever. It is frequently possible to make a strong commercial case for adopting such tools.
Improved economy of scale: Since data entry and processing can be done automatically, streamlining software will probably result in a reduction in the amount of paper used in your business and a need for less workers. Your company will probably save money as a result, allowing you to devote funds elsewhere.
Increased Effectiveness: When procedures are streamlined and employees can more clearly understand the daily responsibilities and expectations placed upon them, productivity among your staff members is likely to increase. When superfluous chores are decreased, they will be better able to concentrate on the calibre of the work they are creating.
Better communication: Improved departmental communication and better work tracking are two benefits of streamlined management systems. Employees will be able to complete given duties more quickly since they will spend less time traveling around to speak with one another.
More Efficient Use Of Time: You and your staff will probably be better able to manage your time, do the most crucial work first, and have buffer time in between tasks if there are fewer tedious chores for you and them to perform.
Reduce risk: Streamlining procedures increases transparency for businesses. From a single spot, it is simpler to monitor your employees' progress and identify errors or missed deadlines. For instance, streamlining might assist in meeting company duties like following regulations or providing clients with a product or service on time that you may manufacture.
The best inventory management program for your company will rely on a number of elements, including your financial situation, the nature of your industry, and particular features like mobile apps and cloud backup.
Tracking, auditing, and reordering inventory are key processes in managing the goods that come into and go out of your firm. You can maintain your shelves filled with the goods that keep your consumers coming back if you use the right inventory management techniques and technologies. You can make sure your staff is working efficiently and generating the maximum revenue possible at the same time.